The answer is a resounding yes! But does the result measure up? I’ll give it a go for the first time.
Silver brazing
This is a new technique for me, because although I’ve done quite a bit of soldering with tin, the objective here is quite different.
It’s a technique that’s often used in jewellery, and it has to meet two main requirements: strength and aesthetics. Suffice to say that on this first attempt, I had no ambitions regarding this second criterion.
To solder with silver you need at least :
- a torch. I’m giving it a go with a kitchen torch.
- flux, to strip and protect the brazing area from oxidation. I used IT3P, which can be used from 550 to 880°C.
- silver solder. I chose to use a weak brazing strip (melting range 705-725°C).
- a brazing support.
Weak solder, strong solder? It’s almost a detail for this test, but as I’d like to try to assemble enamelled elements, the braze must melt before the enamel.
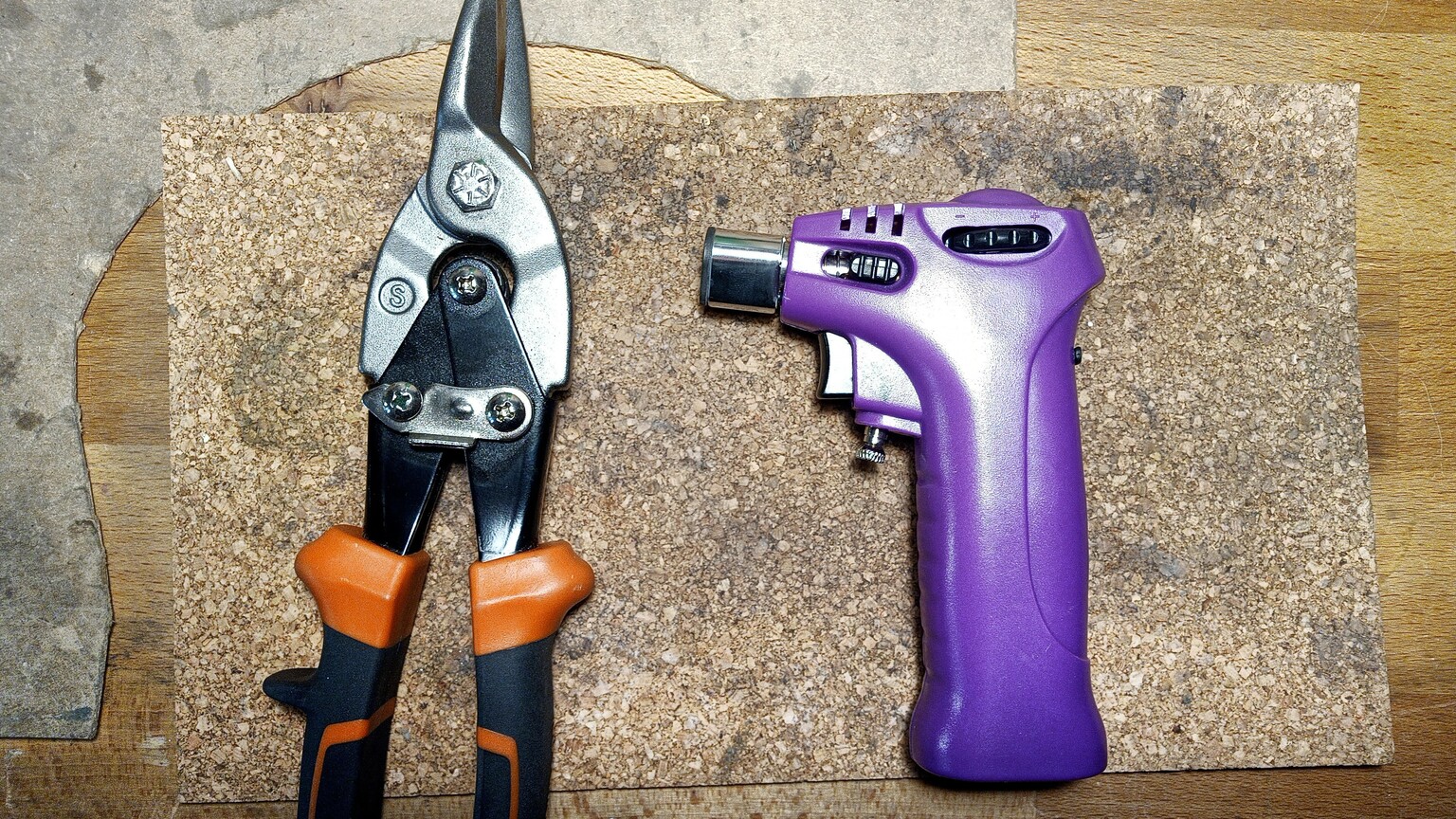
Zinc shears to cut the brazing mat, a kitchen torch to melt it
The protocol
- I cut two sections of stainless steel stud wire and sand the ends at approximately 30° to increase the brazing surface;
- I spread flux paste over the two areas to be brazed;
- I cut a small straw from the brazing strip;
- I position this straw between the two ends, which I bring as close together as possible;
- using the torch, I heat the area to be soldered; I stop as soon as the solder has melted.
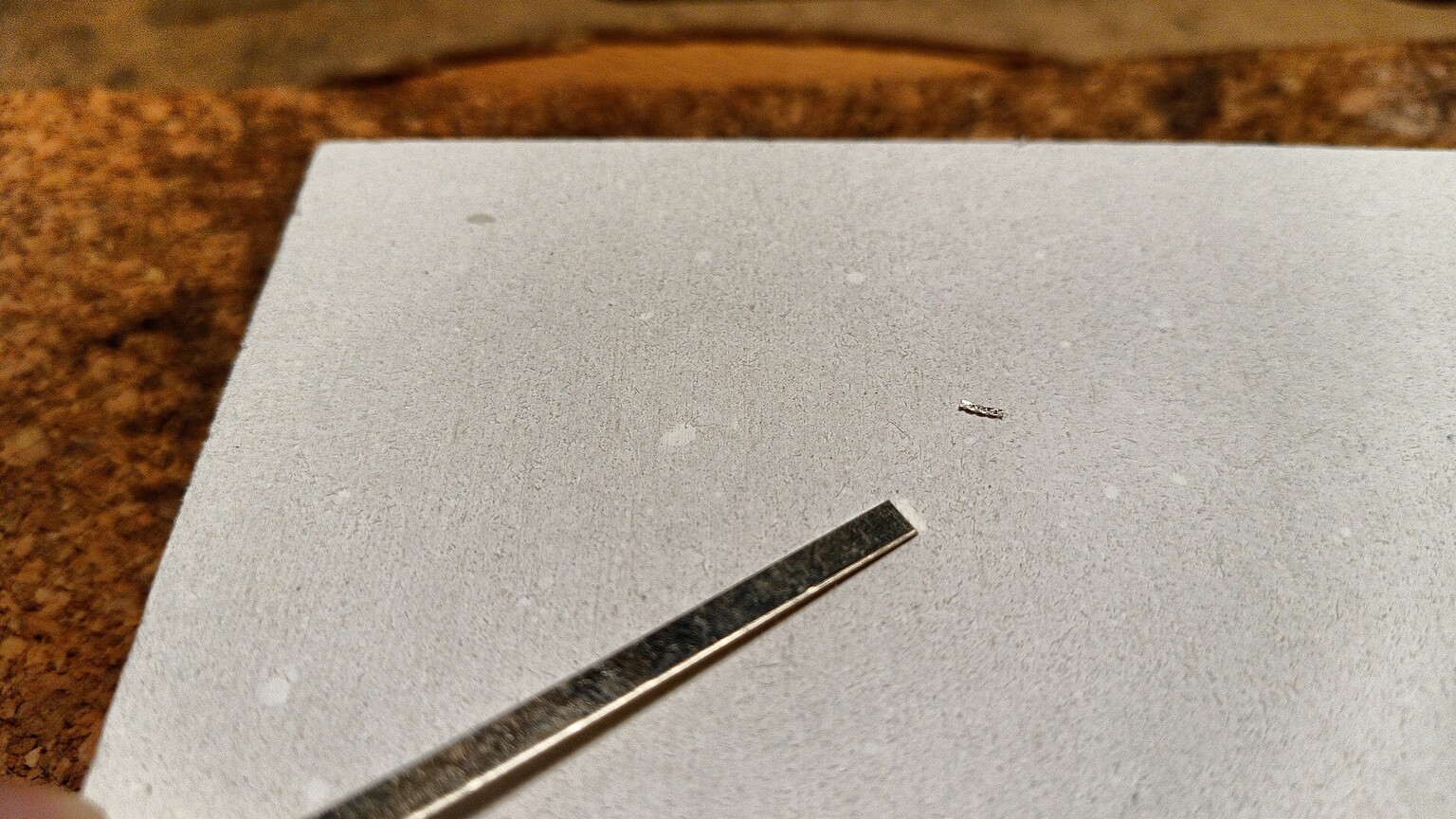
A straw of silver solder cut with shears
The result?
I have to admit, I had to make two successive attempts. I think that in the first case, I had skimped on the flux.
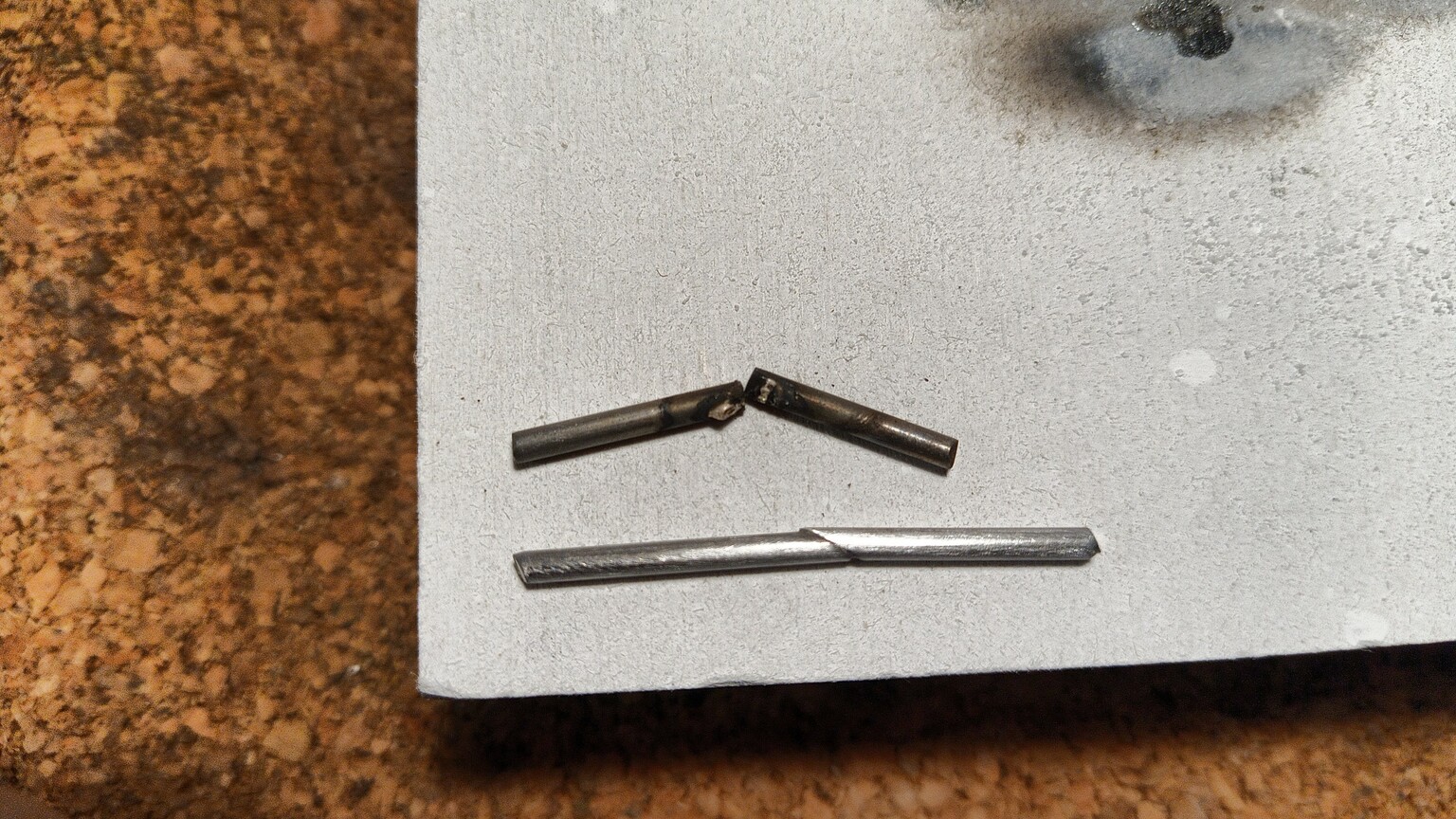
Two silver brazing tests
My second attempt isn’t pretty, but it seems to be holding! To find out for sure, I improvise a little test: place the brazed stainless steel wire in a vice, and bend it with pliers to check that the joint is strong enough.
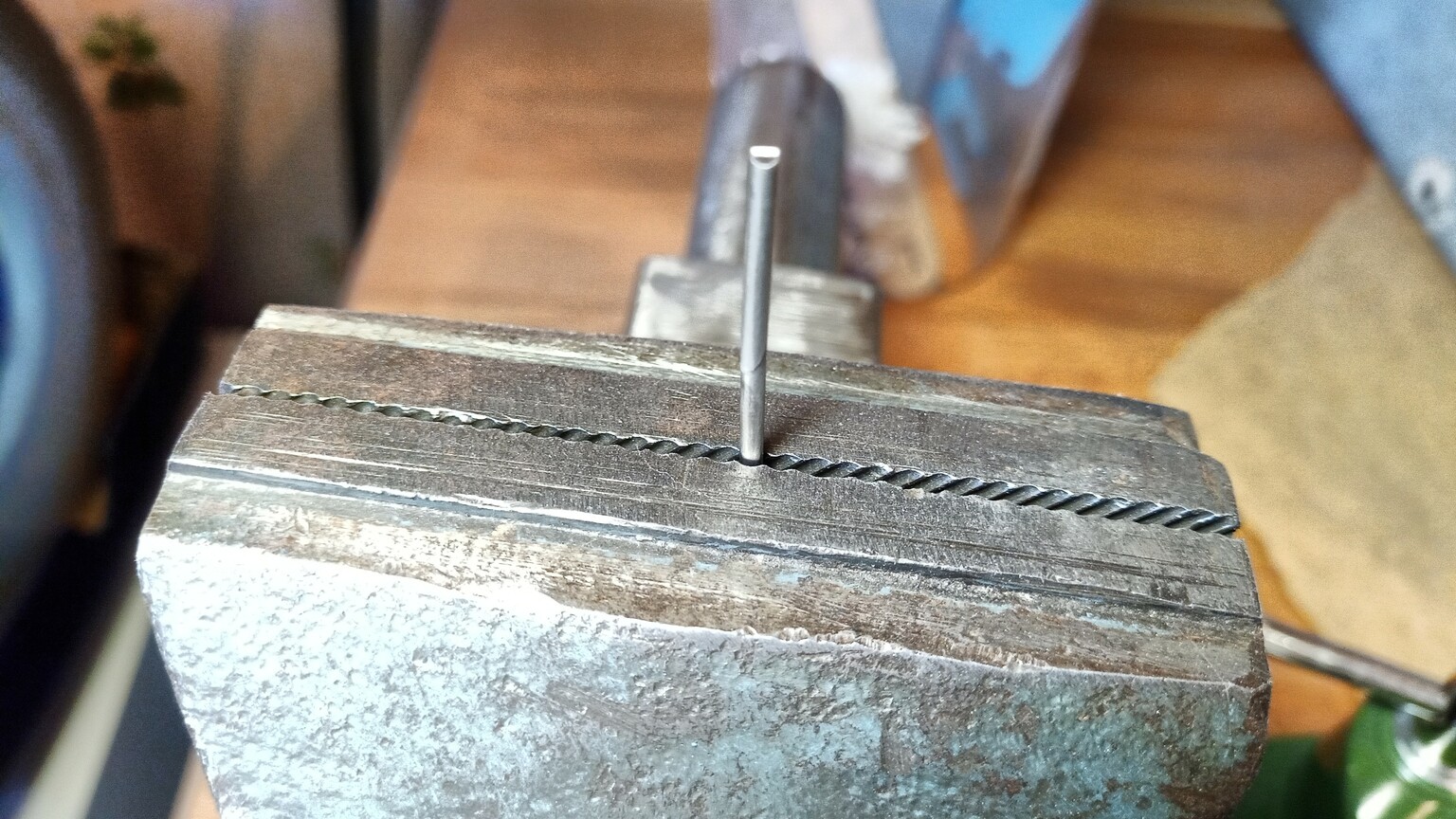
The stainless steel wire is positioned in the vice
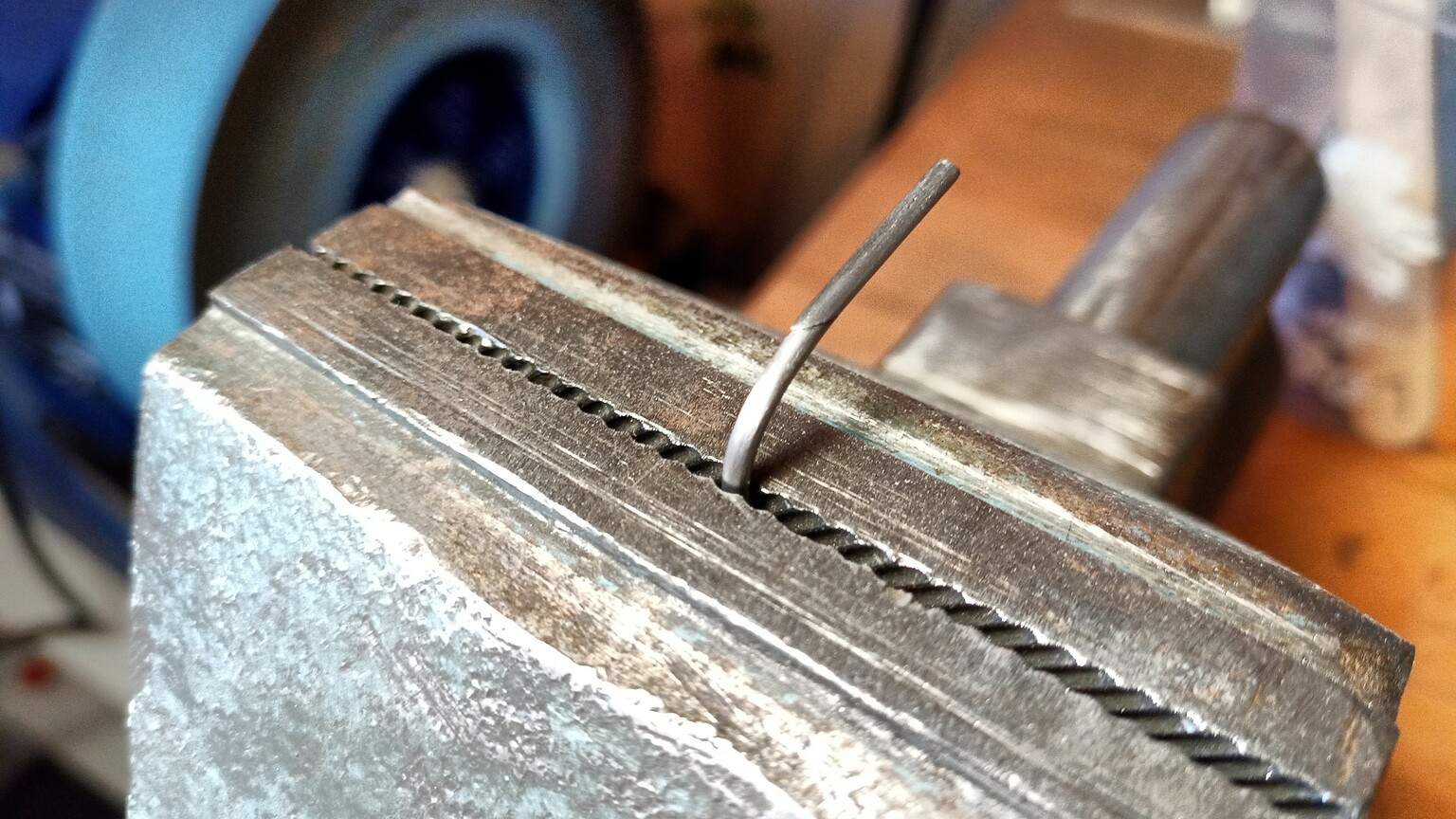
Stainless steel wire after twisting with pliers
It’s resisting! And I should point out that 2.4mm dowel wire is not garden wire :)
Conclusion
This is excellent news, especially as I don’t plan to braze mechanical parts that have been put through a lot of hard work. The technique is simple. As always, it will take practice to do a good job, but it’s encouraging. Now I’ve got to get on with assembling enamelled parts without ruining everything!